Industrial concreting has played a pivotal role in shaping modern infrastructure from massive skyscrapers to intricate bridges, the versatility and durability of concrete have made it a cornerstone of industrial development. This article explores the evolution, techniques, and impact of industrial concreting, highlighting its significance in today’s construction landscape.
The history of industrial concreting brisbane dates back to ancient civilizations, with early forms of concrete used by the Romans to build structures like the Pantheon. However, the Industrial Revolution in the 19th century marked a turning point, as advancements in technology and materials enabled the mass production and widespread use of concrete. The introduction of Portland cement, invented by Joseph Aspdin in 1824, was a game-changer, providing a reliable and high-quality binding material that revolutionized construction practices.
One of the key developments in industrial concreting was the invention of reinforced concrete. By embedding steel bars within concrete, builders were able to overcome its inherent weakness in tension, resulting in a composite material with exceptional strength and flexibility. This innovation paved the way for the construction of taller and more complex structures, such as skyscrapers and long-span bridges, transforming urban landscapes and enabling the efficient use of space.
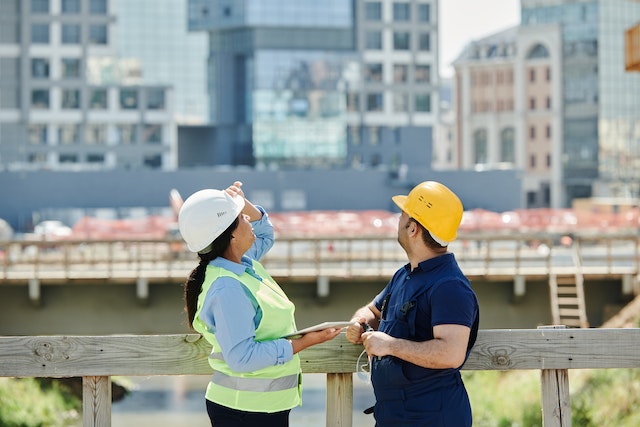
The techniques and processes involved in industrial concreting have evolved significantly over the years. Modern concrete production involves a precise combination of cement, aggregates, water, and additives, mixed in specific proportions to achieve desired properties. Advanced machinery, such as concrete batching plants and transit mixers, ensures consistent quality and efficiency in large-scale projects. Additionally, innovations like self-consolidating concrete, which flows and settles under its weight, have simplified the placement process and reduced labour requirements.
Formwork, the temporary mould into which concrete is poured, has also seen remarkable advancements. Traditional wooden formwork has largely been replaced by modular systems made from materials like aluminium and steel, which offer greater durability, ease of assembly, and reusability. The use of prefabricated formwork panels and automated formwork systems has streamlined construction processes, allowing for faster project completion and cost savings.
One of the most significant impacts of industrial concreting is its contribution to the development of infrastructure. Concrete is the primary material used in the construction of highways, bridges, tunnels, dams, and airports, providing the foundation for transportation networks and facilitating economic growth. The durability and low maintenance requirements of concrete structures make them ideal for infrastructure projects, ensuring long-term sustainability and reducing the need for frequent repairs.
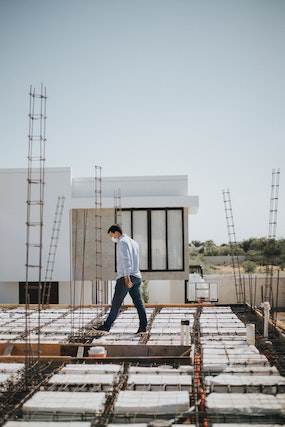
Industrial concreting has also played a crucial role in urbanization. The ability to construct high-rise buildings and large-scale residential complexes has addressed the challenges of population growth and urban density. Concrete’s fire resistance, sound insulation properties, and thermal mass contribute to safer and more comfortable living environments. Moreover, the use of precast concrete elements, manufactured off-site and assembled on-site, has accelerated construction timelines and minimized disruptions in urban areas.
The production of concrete has a significant environmental footprint, primarily due to the energy-intensive process of cement manufacturing and the associated carbon emissions. However, the industry has made strides in developing eco-friendly alternatives. Supplementary cementitious materials, such as fly ash, slag, and silica fume, are increasingly used to partially replace Portland cement, reducing greenhouse gas emissions and improving the overall sustainability of concrete.